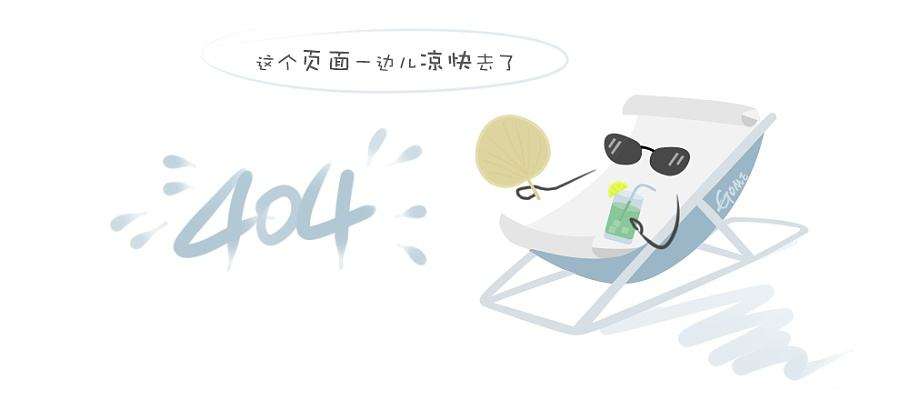
沧州大化党委书记、董事长谢华生在控制中心指导数字化转型工作
作为我国民族聚氨酯、聚碳酸酯产业的重要一员,沧州大化集团有限责任公司通过“数字大化”建设,深入推进管理变革创新,深挖数据资源价值和潜力,探索出一条数字化转型之路。
“沧州大化tdi及聚碳酸酯生产工艺复杂,操作变量多,但生产运行和设备管理主要靠人工控制,不具备数据驱动下的风险管控能力;产品工艺流程由多个装置单元分别进行管理控制,缺少一体化的协调和指挥,协同能力差;同时面对复杂的工艺条件,员工能力不足、工作效率低下的弊端日益显现,迫切需要以智能化升级突破瓶颈。”公司党委书记、董事长谢华生回忆公司数字化转型的起步之艰、行路之难,充满了感慨。肩负着发展使命的沧州大化,就在这样的艰难中,义无反顾地踏上了征程。
颠覆传统精简组织架构
沧州大化颠覆了传统化工企业的思维和管理模式,为化工企业实现基于数字化转型的扁平高效管理提供了最新范本。通过成立应急(运营)指挥中心等一系列举措,纵向构建三级(决策中心、调度中心、操作员)管理模式,消除执行偏差,大幅提升工作效率;横向拓展整合优势资源,实现系统集成优化,跨公司、跨产品、跨专业实施供产销一体化管理。
一是生产系统内取消装置和值班经理建制,控制中心设调度和操作员两个岗位,将全部监控点和控制点按照重要程度分配到相应岗位,责任到人、控制点位到人。二是成立应急(运营)指挥中心,集团公司至基层指令下达减少至三级,即应急(运营)指挥中心、调度员、操作员。应急(运营)指挥中心代表集团公司下达安全生产及商务运营调度指令,实现全方位、全流程的系统集成、协同高效,最大限度优化运营、创造效益。
沧州大化改变了原有的以产定销的老模式,各个单元联动形成合力,使生产紧紧地跟着市场走。应急(运营)指挥中心作为组织、协调和指令下达部门,每天组织召开生产运营协调会,在对产品市场进行准确预判的基础上,确定工艺系统运行的负荷,进而确定原材料的采购数量,确保实现效益最大化。
量身定制推进“三化”管理
沧州大化创新企业管理模式,将信息化、物联网和大数据技术应用于化工生产管理之中,推进“三化”管理,从多个层面实现企业高效管理并全面保障化工生产安全。
一是决策指令化。化企决策信息往往以电话或者会议的形式传达,指令笼统、不精确,在执行过程中易出偏差。智能化升级后,沧州大化从应急(运营)指挥中心开始,各层级决策自上而下逐级在线下达数据明晰的调度指令,并自下而上逐级反馈指令执行情况,实现了精准决策。
二是指令表单化。为确保指令准确落地,沧州大化各个层级所下达的指令全部以表单化的形式下达,杜绝了口头传达或以文件传达文件存在的弊端。同时,集团公司创新工作部对表单化执行情况进行统一管理和考核,并定期进行讲评。
三是表单数字化。各层级全部以数字化形式下达指令表单,精确到“什么时候开始、进行哪些操作、具体调整到多少、什么时间内调整完毕”。操作员在mes中获取指令信息、指标偏离信息和操作指导信息,在dcs中进行操作调整,确保操作精准无误,指令执行无任何偏差。操作完成后,在系统自动显示“完成”。
为确保决策指令精准落地,沧州大化数字化指标全部实现实时在线,所有报警、指令、提示信息等都以管理看板的形式在控制中心大屏实时展示,实现了信息共享。一线员工可以清楚掌握公司相关管控信息,确保无偏差执行。
优化生产打造智能工厂
通过数字化转型,沧州大化逐步建立智能管控新模式,不断优化生产系统,转变生产运行管理模式,提升生产运行水平,进而提高了安全生产、环保管控水平和盈利能力。
实施异常管控,最大程度降低劳动强度和复杂程度。沧州大化独立开发总控智能辅助系统(aoas),用于辅助总控岗位进行dcs监盘,监盘效率提高300倍,操作频次从174次/小时减至26次/小时;通过对装置自控回路进行整定和分析,自控率由97%提高到99.8%,为实施异常管理打下了基础。为确保生产安全稳定运行,沧州大化自主实施报警表、偏差表、指令表“三张图表”管理模式,以此为依托,将运行指标分为红、橙、黄、绿四个区域,通过趋势变化和aoas系统提示,可以提前发现生产问题、预判设备运行状态,同时大幅减少分析检测项目,实现安全、稳定和优化运行。而总控操作人员只需关注报警指标并进行处置,劳动强度大幅降低,为准确实施异常管控提供了保障。
建立基于数字化的设备全生命周期管理。沧州大化改变原有的分专业管理和计划检修模式,将设备的档案、检修、备件等静态信息和振动、温度、电流、巡检、工艺指标异常等动态信息进行整合和关联,形成数字化设备状态评估结果,通过数据动态掌握设备运行状态,实施预防性维护,实现设备的一体化管理;建立了可视化智能化巡检新模式,对巡检线路和巡检任务实施标准化管理,巡检信息通过数字、图片和视频等形式,同步向控制中心人员和各相关专业管理人员推送,多角度进行巡检情况分析和判断,实现了现场巡检管理的标准化、规范化和数字化。
数字评价,彻底消除人为干预因素。沧州大化建立了以不变价成本为核心的生产绩效评价系统,以不变价指标数据反映生产运行整体情况,通过层层数据分析查找生产运行中存在的问题,每一个关注点、每一个管理环节都有数据做支撑,改变了原有以定性为主的绩效评价模式,建立了数字化动态定量评价模式,通过自动生成的不变价成本指标数据进行月度评价,并与薪酬挂钩;通过当班结束后自动生成的运行绩效数据,实现班组绩效数据的动态展示。数字评价体系的应用,对生产系统实现“安稳长满优”运行起到了至关重要的作用。
商务业务全流程实现数字化管理。沧州大化销售、生产、物流、财务等管理和业务人员处于同一数据平台中,形成了一个有机整体,通过建立全商务链数字化平台,建立了从订单建立、核算审批、货款核对、车辆安排、出库称重、物流跟踪、货到签收到结算开票的全业务链、全自动化、无缝连接的数字化管控流程。
“数字化转型让沧州大化产生了‘化学变化’,本质安全水平大幅提升,职工劳动强度和工作复杂程度大幅降低,装置运行更安全、稳定,管理流程更高效,人力资源更优化,为企业转型升级和可持续发展打下坚实基础。”谢华生说。